Table of Contents
What is a Gyratory Crusher?
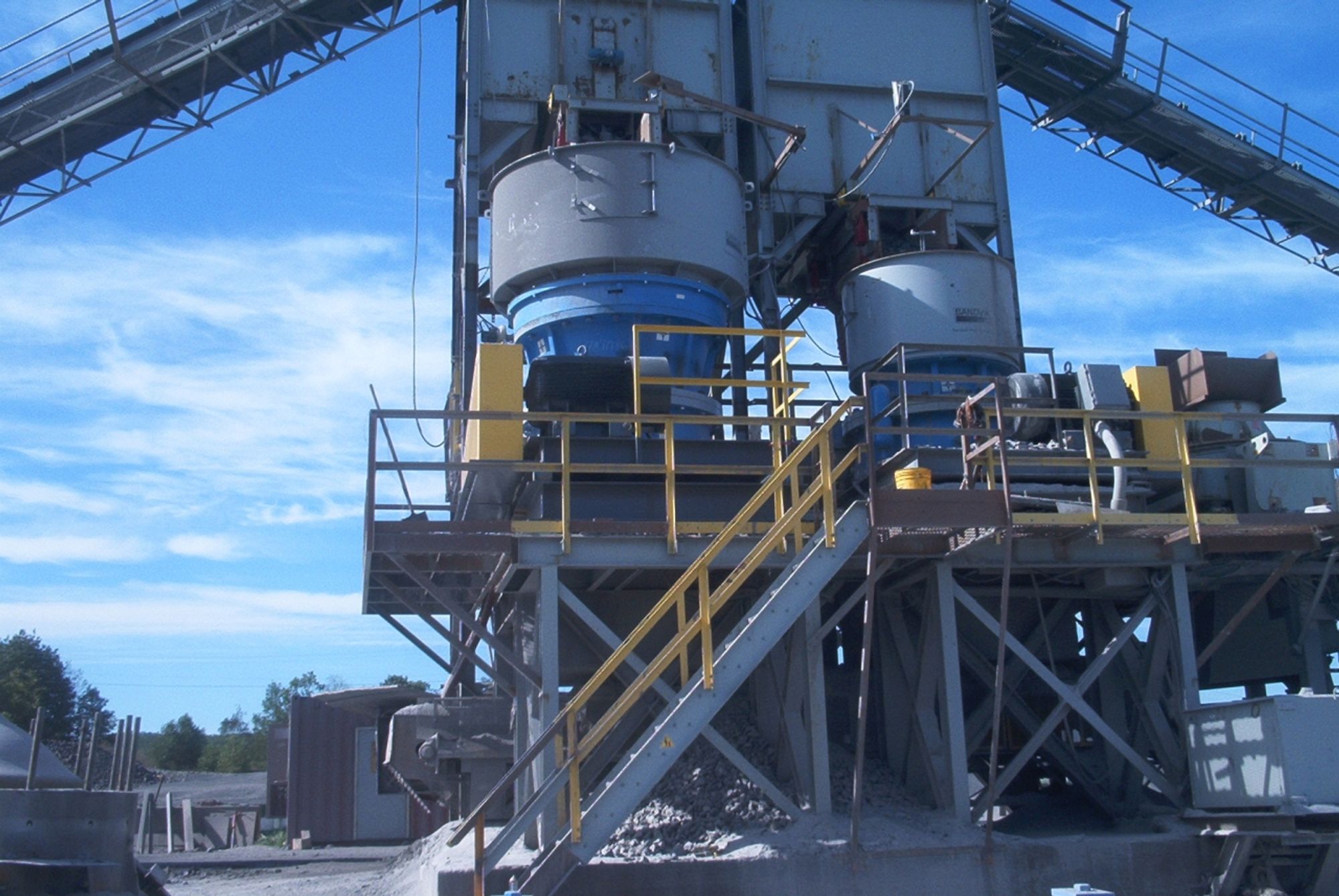
A gyratory crusher is a type of crusher that uses a cone-shaped crushing head mounted on a spindle to break rock material. It is typically used in the aggregate industry, where it is used to crush rock and other materials. The crushing head is driven by a vertical shaft that rotates within a fixed concave bowl. As the rock is fed into the top of the crusher, it is crushed between the crushing head and the concave bowl. The gyratory motion of the crushing head allows it to crush the rock by continually moving it closer to the concave bowl until it is small enough to fall through the bottom of the crusher. This process continues until all of the rock has been crushed to the desired size.
Gyratory Crusher vs Jaw Crusher vs Cone Crusher
Gyratory crushers, jaw crushers, and cone crushers are all commonly used in the aggregate industry to crush rock material. Each of these types of machines have their own unique characteristics and have been designed for specific applications.
Gyratory crushers use a cone-shaped crushing head that is mounted on a spindle to break rock material. This type of crusher is typically used in the primary stage of rock crushing, and is capable of crushing materials with a high compressive strength. They are typically used for hard, abrasive materials.
Jaw crushers use a pair of steel jaws to crush rock material. One jaw is fixed in place, while the other moves back and forth to break the rock. Jaw crushers are typically used for primary crushing, and are able to handle smaller and softer materials than gyratory crushers.
Cone crushers use a rotating cone-shaped crushing head to break rock material. They are similar to gyratory crushers, but are typically used in the secondary or tertiary stage of rock crushing. They are capable of producing fine-grained aggregates with a high compressive strength.
In summary, gyratory crushers are used in the primary stage of rock crushing, jaw crushers are used in the primary and secondary stages of rock crushing, and cone crushers are used in the secondary and tertiary stages of rock crushing. Each of these types of machines has its own unique characteristics and are designed for specific applications.
Considerations with Gyratory Crushers
When setting up a gyratory crusher, there are several key factors that must be considered. These include:
- The size and type of material that will be processed by the crusher. The size and type of material will determine the size and type of crusher that is required.
- The capacity of the crusher. The capacity of the crusher will determine how much material can be processed in a given time period. It is important to select a crusher with a capacity that is appropriate for the intended application.
- The location of the crusher. The location of the crusher will determine its accessibility and the ease with which it can be serviced and maintained.
- The power source for the crusher. The crusher will need to be powered by an appropriate power source, such as an electrical outlet or a generator.
- The required output size of the crushed material. The output size of the crushed material will determine the size and type of screens and other components that are needed in the crushing circuit.
By considering these factors, you can ensure that the gyratory crusher you select is appropriate for your application and will operate efficiently and effectively.
What materials work best with Gyratory Crushers?

A gyratory crusher can handle a wide range of materials, including rock, gravel, and slag. It is commonly used in the mining industry to crush rock material. The crusher's cone-shaped crushing head is capable of breaking down hard, abrasive materials, such as granite, limestone, and other materials with a high compressive strength. The gyratory motion of the crushing head allows it to crush these materials effectively and efficiently. Gyratory crushers are also capable of crushing softer materials, such as coal and other friable materials, but they are not typically used for these materials.
Maintenance
To maintain a gyratory crusher in the aggregate industry, it is important to regularly monitor and inspect the following parts of the crusher:
- Maintain the crusher's lubrication system by regularly checking and adding oil as needed. This will help to ensure that the crusher's moving parts are properly lubricated, which can help to extend their lifespan.
- Regularly inspect the crusher's belts, pulleys, and other drive components for signs of wear or damage. Replace any damaged parts as needed to keep the crusher running smoothly.
- Inspect the crusher's crushing chamber for any signs of wear or damage, such as cracks or other damage to the crushing head or concave bowl. Replace or repair any damaged parts as needed.
- Monitor the crusher's feed rate and adjust it as needed to ensure that the crusher is running at its optimal capacity.
- Regularly check the crusher's discharge chute for any blockages or other issues that may prevent the crushed material from being discharged properly.
By regularly maintaining and inspecting your gyratory crusher, you can help to ensure that it continues to operate at peak performance and provide a high-quality, consistent output of crushed material.