Heavy equipment is used in the aggregate mining industry to help move and manipulate large pieces of earth. Heavy equipment such as front-end loaders, bulldozers, backhoes, and dump trucks are used to move the earth and large rocks from one location to another. Heavy equipment is also used to move ore, soil, and other materials from one part of the mine to another. Additionally, heavy equipment is used to facilitate the mining process, such as drilling and blasting.
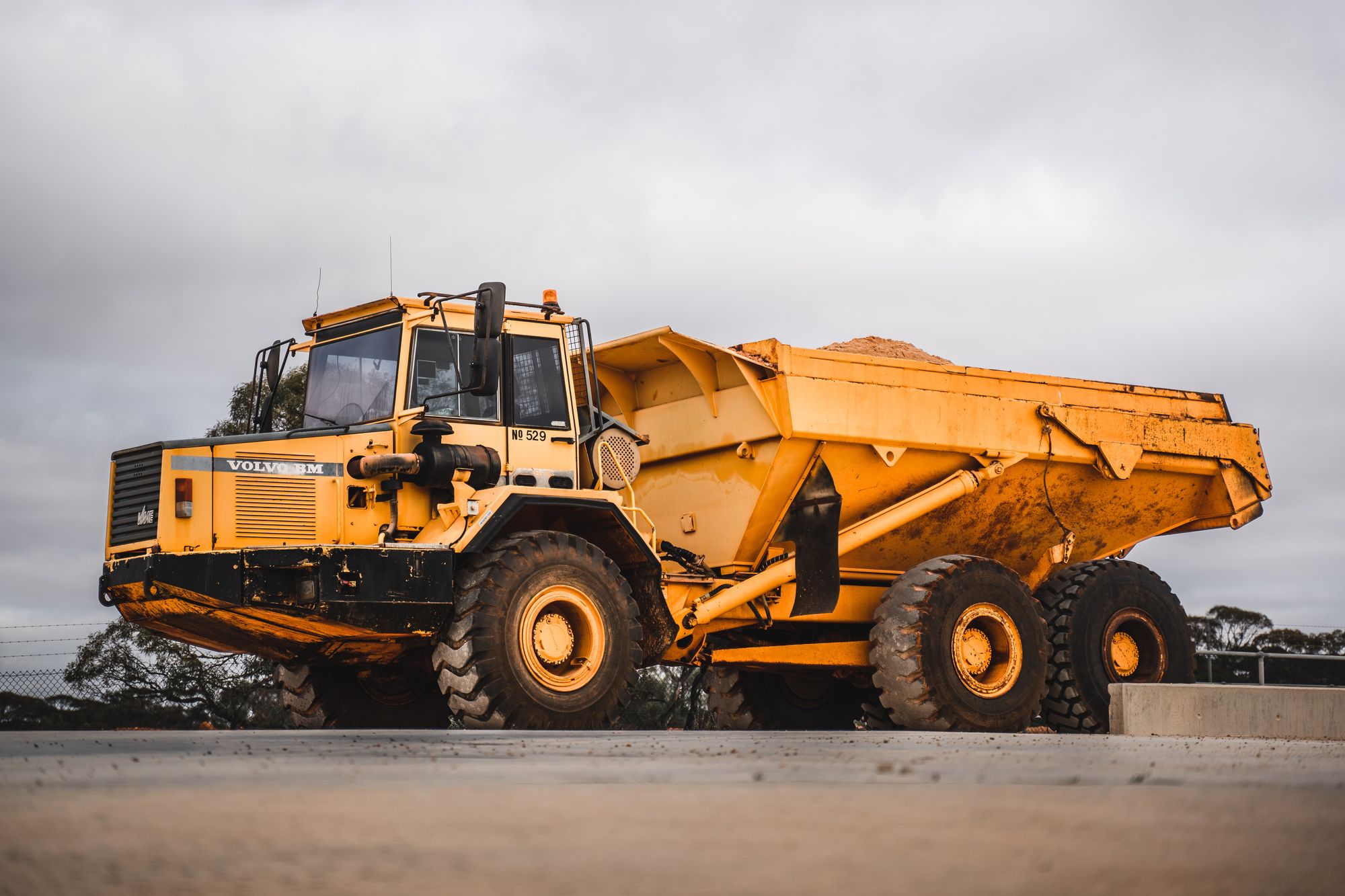
Heavy Equipment Inspection Best Practices
The importance of regular inspections for heavy equipment cannot be overstated. Regular inspections are essential to ensure the safety of workers and the quality of the equipment. Here are some of the best practices for heavy equipment inspections.
- Use Checklists: Checklists are a great way to ensure that all of the necessary inspections are completed. Checklists should include all of the components of the equipment that need to be inspected, as well as any safety protocols that should be followed. This will help to ensure that nothing is missed during the inspections.
- Document Findings: It’s important to document the findings of the inspections. This will help to establish a record of the status of the equipment, which can be used for future reference.
- Follow Manufacturer Guidelines: Different types of heavy equipment may have different inspection requirements. It’s important to follow the manufacturer’s guidelines for each piece of equipment to ensure that the inspections are thorough and effective.
- Be Vigilant: Heavy equipment inspections should be conducted on a regular basis. It’s important to be vigilant and look for any signs of wear or damage that could potentially lead to an accident. It’s also important to take note of any changes in the equipment’s performance, as this could indicate a potential issue.
- Report Issues: If any issues are found during the inspections, they should be reported immediately. This will ensure that the issue is addressed in a timely manner and can prevent any potential accidents or further damage.
By following these best practices, companies can ensure that their heavy equipment is properly inspected and maintained. This will help to keep workers safe and the equipment functioning at its best.
Heavy Equipment Maintenance Best Practices
- Follow the manufacturer's maintenance schedule: Make sure to check the manufacturer's recommendations and follow their suggested maintenance schedule. This will help ensure the proper performance of the equipment and extend its lifespan.
- Clean and inspect the machine regularly: Regularly inspect and clean the machine in order to identify any potential issues before they become a problem. Make sure to check the fluids, lubricants, hoses, and belts regularly.
- Change the oil and filters regularly: Change the oil and filters as recommended by the manufacturer or as needed. This will help to keep the engine and other parts running smoothly and efficiently.
- Check the tires regularly: Inspect the tires for any wear and tear and make sure to keep them properly inflated.
- Perform regular safety checks: Regularly inspect the machine for any safety hazards and make sure to follow all safety protocols.
- Regularly inspect and tighten bolts and nuts: Make sure to inspect and tighten all bolts, nuts, and other fasteners regularly. This will help to keep all components in good working condition and avoid any potential issues.
Types of Heavy Equipment
- Excavators: Used for digging and moving large amounts of earth and debris.
- Haul Trucks: Used for transporting large amounts of materials and equipment.
- Loaders: Used for loading, excavating, and transporting materials.
- Dozers: Used for leveling and pushing materials.
- Drills: Used for creating holes for blasting and exploration.
- Crushers: Used for reducing size of mined materials.
- Graders: Used for creating a flat surface and grading materials.
- Shovels: Used for digging and scooping materials.
- Scoops: Used for scooping and lifting materials.
- Pumps: Used for pumping out water
A Culture of Safety
Safety is extremely important in the aggregate mining industry. The industry is inherently dangerous, with miners often working in dangerous and hazardous conditions. Accidents can cause serious injury or even death, so it is essential that workers be aware of the risks and take appropriate steps to protect themselves. By following safety procedures and regulations, miners can reduce the risk of accidents and make sure that the workplace is as safe as possible. Additionally, safety regulations can help protect the environment from potential pollution caused by mining operations.
A culture of safety in the workplace is essential for any organization. It is crucial for creating a safe and healthy environment where employees feel respected and valued. A culture of safety promotes trust, accountability, and communication between employees and management, which leads to improved productivity and morale. It also helps to reduce the risk of injuries, accidents, and other potential hazards. Additionally, a culture of safety can help to prevent costly litigation and other financial losses that can result from unsafe practices or conditions. A culture of safety demonstrates a commitment to the safety of all employees and helps to create an atmosphere of trust and respect.